Digital Twin
Fuel cell monitoring system based on a digital twin architecture reducing system complexity and cost by 40%.
Fuel cell monitoring systems are essential for ensuring the smooth operation and maintenance of fuel cell power generation. However, their implementation can be complex and costly, requiring a large number of sensors, manual data collection and analysis processes.
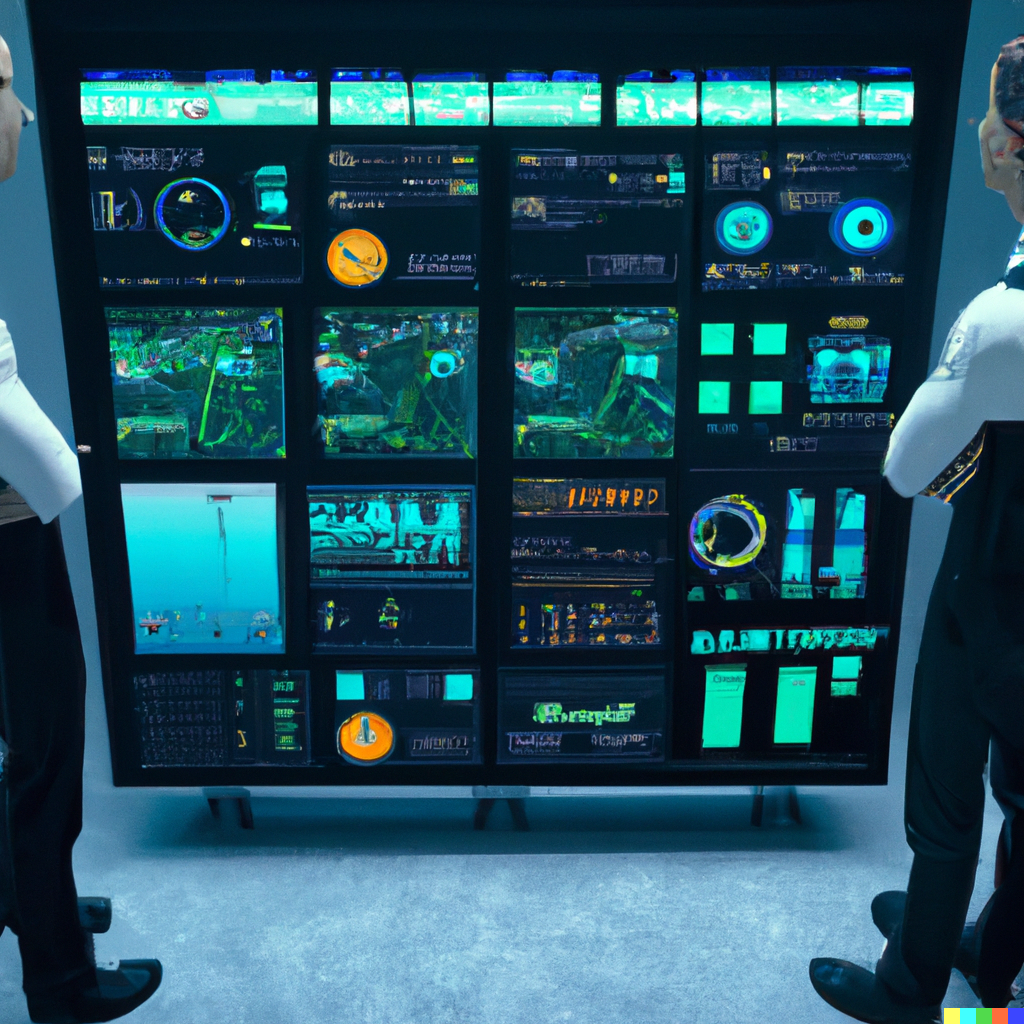
In order to address these issues, we developed a fuel cell monitoring system based on a digital twin architecture. Digital twins are virtual representations of physical systems that can be used to simulate the behavior and performance of the real-world system. By using artificial intelligence prediction algorithms, we were able to create digital twins of the fuel cell system that monitor and predict the health of the system.
One of the key benefits of this approach is that it significantly reduced the complexity not only of the monitoring system but also of the next iteration of the product, resulting in the reduced parts, production and maintenance cost. By replacing sensors with digital twins, we were able to reduce a more streamlined and cost-effective system.
Our solution also includes visualization dashboards that allow users to easily access and interpret data on the health and performance of their systems. This enables organizations to make informed decisions about maintenance and repair needs, helping to ensure that their equipment is operating at optimal levels.
Overall, the use of digital twins architecture, prediction algorithms, graphical user interface and well designed system architecture allowed us to significantly improve the efficiency and cost-effectiveness of our quality monitoring processes. By automating data collection and quality checks, we have been able to free up time and resources for other tasks, allowing organizations to focus on more value-added activities.